Benefits of Sintered Silicon Carbide Ceramic Shaft Sleeves
By:Admin
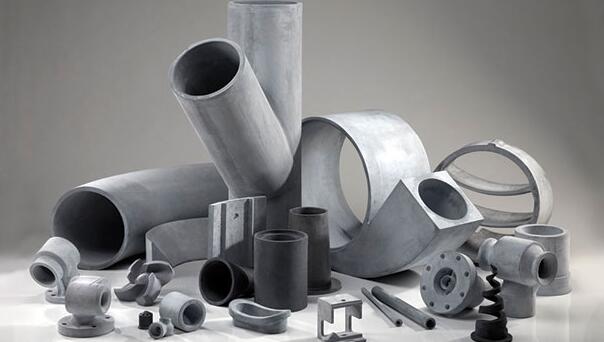
Sintered Sic Shaft Sleeve: The Future of Wear-Resistant Technology
In an industrial setting, machinery components are subjected to a lot of wear and tear, which eventually leads to failure. This is especially true for components like shaft sleeves that come in direct contact with abrasive materials that cause rapid degradation. As a result, industries are constantly seeking materials that can withstand the tough conditions that they operate in, and sintered silicon carbide (Sic) has proven to be the solution.
Sintered Sic Shaft Sleeve, also known as sintered silicon carbide, is a ceramic material that is made by combining silicon carbide powder and a sintering aid using either pressureless sintering or hot pressing. The resulting material is a hard and durable ceramic with exceptional wear and temperature resistance, superb chemical resistance, and great mechanical strength.
The benefits of using Sintered Sic Shaft Sleeve in industrial machinery cannot be overstated. The material is highly wear-resistant, with a hardness of 9.0 on the Mohs scale, which is second only to diamonds. It can withstand high temperatures of up to 1600°C without degrading, which make it ideal for use in high-temperature applications. Additionally, it has excellent resistance to corrosion and chemical attack, making it perfect for applications that require contact with corrosive or acidic materials.
One of the pioneers of Sintered Sic Shaft Sleeve technology is a US-based company, which has been producing the material for over thirty years. According to the company, the success of the material lies in the precise control of the sintering process, which ensures uniform and consistent properties throughout the material. The company boasts a wide range of Sintered Sic Shaft Sleeve products that are tailor-made to meet the diverse needs of their clients.
Sintered Sic Shaft Sleeve is suitable for use in various industrial and chemical processes, including power generation, pumping, mining, and chemical processing. In pumps, it is used as a seal ring to prevent leakage between the pump shaft and the casing, thereby reducing maintenance costs and downtime. In mining, it is used as a lining material for cyclone separators that separate the valuable minerals from the ores, improving efficiency and productivity.
In the chemical process industry, Sintered Sic Shaft Sleeve has proven to be invaluable in reactors and distillation columns that require contact with highly corrosive chemicals. The material has exceptional resistance to acids, alkalis, and organic solvents, making it ideal for such applications.
In conclusion, Sintered Sic Shaft Sleeve is a game-changing material for industrial applications. Its exceptional properties make it the ideal material for heavy-duty machinery components that are subjected to harsh operating conditions. Companies that use this material can reduce maintenance costs, improve equipment reliability, and increase productivity. As the demand for high-performance industrial components continues to grow, the use of Sintered Sic Shaft Sleeve will become even more prevalent, and its many applications will continue to expand.
Company News & Blog
Guide on selecting suitable chute liner for optimal performance
Choosing the right chute lining material is an essential step during the design consideration process. The selection of a suitable chute lining material can significantly impact the performance, durability, and maintenance requirements of the chute. In this blog post, we will discuss the importance of choosing the right chute lining material, specifically for coal chutes. Additionally, we will explore various factors that should be taken into account when selecting coal chute lining materials.Coal chutes are used in industries such as mining, steel, power generation, and cement manufacturing, where coal needs to be transferred from one location to another. These chutes are subjected to extreme conditions, including high abrasion, impact, and temperature variation. Therefore, it is crucial to choose a chute lining material that can withstand these challenges and provide maximum longevity.When selecting a chute lining material for coal chutes, the following factors should be considered:1. Abrasion resistance: Coal is a highly abrasive material and can cause significant wear and tear on chute surfaces. Therefore, the lining material should have excellent abrasion resistance to ensure prolonged service life.2. Impact resistance: Coal can also cause impact damage to chute surfaces, especially during the loading and unloading process. The lining material should possess good impact resistance to withstand such forces without cracking or breaking.3. Temperature resistance: Coal chutes are often exposed to high temperatures due to the combustible nature of coal. Therefore, the lining material should be able to withstand elevated temperatures without undergoing any structural or chemical degradation.4. Corrosion resistance: Coal contains sulfur and other corrosive elements that can lead to corrosion of metal chutes. Hence, it is advisable to choose a lining material that has excellent corrosion resistance properties to prevent any damage or deterioration of the chute structure.5. Material flow properties: The lining material should possess a smooth surface to promote the smooth flow of coal through the chute. Any rough surfaces or protrusions can cause material hang-ups or blockages, leading to production inefficiencies.Considering these factors, ceramic chute lining materials are often preferred for coal chutes due to their exceptional properties. Ceramic materials, such as alumina ceramics, offer superior abrasion resistance, impact resistance, and temperature resistance. They are extremely hard and can withstand the abrasive nature of coal, reducing wear and tear significantly. Alumina ceramics also have excellent high-temperature resistance, ensuring the longevity of coal chutes in industries where coal combustion occurs.Moreover, ceramic chute linings provide excellent corrosion resistance, eliminating the concerns related to corrosion caused by the sulfur content in coal. Their smooth surface properties help in reducing material hang-ups or blockages, improving the material flow efficiency. Additionally, ceramic linings can be easily customized and installed to fit specific chute designs.In conclusion, the selection of the right chute lining material is of utmost importance when designing coal chutes. Considering factors such as abrasion resistance, impact resistance, temperature resistance, corrosion resistance, and material flow properties, ceramic materials, especially alumina ceramics, are an excellent choice for coal chute linings. Their exceptional properties ensure extended service life, reduced maintenance requirements, and improved production efficiency. If you are looking for high-performance chute lining materials for your coal chutes, consider ceramic options to provide you with a reliable and long-lasting solution.
High-Quality Ceramic Glass Tube Radiant Heaters for Refrigeration and Heat Exchange Parts in India
Glass, India, Refrigeration, Heat Exchange Parts, Bomac Electric Limited.Introduction:Heating is an essential aspect of modern-day industries, and radiant tube heaters have been the favorite choice for many years. Ceramics have been a popular material for radiant tube heaters due to their excellent thermal insulation properties and their capability to resist high temperatures. Ceramics are also very durable and have a longer lifespan. India is a prominent market for Radiant Tube heaters, and Bomac Electric Limited is a trusted seller of ceramic glass tube radiant heaters.Features of Ceramic Glass Tube Radiant Heaters:Ceramic Glass Tube Radiant Heaters are a popular choice for industrial heating applications. They are known for their outstanding heat transfer properties and their superior resistance to thermal and environmental stresses. They are highly efficient and cost-effective and are often used in heating systems where high-temperature heating is required. Here are some of the features of Ceramic Glass Tube Radiant Heaters:1. High Heat Transfer Efficiency: Ceramic Glass Tube Radiant Heaters have excellent heat transfer properties, making them highly sought-after for high-temperature heating applications. The ceramic glass material provides excellent insulation, ensuring that the heat is transferred efficiently while minimizing heat loss.2. High Temperature Resistance: Ceramic Glass Tube Radiant Heaters are capable of withstanding high temperatures with ease. They can operate at temperatures up to 1200°C without failing.3. Durable and Resilient: The ceramic construction of the radiant tube heaters makes them more robust and more durable than standard heating elements. They can withstand harsh environments, vibration, and thermal shock without cracking or breaking.Bomac Electric Limited - India Refrigeration and Heat Exchange Parts:Bomac Electric Limited is a renowned manufacturer and supplier of a vast array of heating products and accessories. They have been in the business for more than 20 years and have established themselves as a trusted and reliable supplier of industrial heating solution providers in India.They specialize in manufacturing and supplying ceramic glass tube radiant heaters, which are highly efficient and cost-effective. Their radiant tube heaters are designed to meet the needs of various industrial sectors, including the automotive industry, chemical plants, and food processing plants.Bomac Electric Limited provides high-quality ceramic glass tube radiant heaters for industrial purposes. They use high-quality materials to ensure that their products meet the standards expected of them. They also provide customization options to clients who need specific requirements.Conclusion:Ceramic Glass Tube Radiant Heaters are essential heating components in industrial settings. They are highly efficient, durable, and capable of withstanding harsh environments. Bomac Electric Limited is a reliable supplier of these heaters in India and has established itself as a respected and trustworthy supplier of heating solutions. If you are looking for radiant tube heaters for your industrial needs, Bomac Electric Limited is a safe bet. Their products are of high quality, and they provide excellent customer service.
Top Silicone Nitride Ceramic Heating Tablet Suppliers and Manufacturers in China for Mutual Benefit Future
Silicon Nitride Ceramics: The Future of Heating TabletsIn the world of electronics, ceramic heating tablets have become a popular choice for manufacturers due to their excellent thermal stability and high mechanical strength. Among these ceramics, Silicon Nitride (Si3N4) is emerging as a super material with unique properties, which makes it a perfect candidate for heating tablets. In this blog, we will explore why Silicon Nitride Ceramics are the future of heating tablets and their advantages over other materials.What are Silicon Nitride Ceramics?Silicon Nitride Ceramics are a type of advanced ceramic that has excellent mechanical properties, such as high hardness, wear resistance, and toughness. It has a unique crystal structure, which enables it to have a high-temperature capacity, low coefficient of thermal expansion, and excellent thermal shock resistance. Silicon Nitride Ceramics are made by sintering silicon nitride powder at high temperatures in the presence of a sintering aid.Advantages of Silicon Nitride Ceramics in heating tablets1. High thermal conductivity: Silicon Nitride Ceramics have a high thermal conductivity of up to 100 W/mK, which ensures efficient dissipation of heat generated by the heating elements. This results in faster heating times and ensures uniform heat distribution across the heating tablet.2. Excellent thermal shock resistance: Silicon Nitride Ceramics have outstanding thermal shock resistance, which means they can withstand sudden temperature changes without cracking or degrading. This makes them ideal for heating tablets that are subjected to rapid temperature changes.3. Corrosion and oxidation resistance: Silicon Nitride Ceramics are chemically inert, which makes them highly resistant to corrosion and oxidation. This makes them perfect for use in heating tablets that are exposed to corrosive or oxidizing environments.4. Low thermal expansion: Silicon Nitride Ceramics have a low coefficient of thermal expansion, which means they do not expand or contract much with temperature changes. This makes them ideal for heating tablets that require stable thermal properties over a wide temperature range.5. High mechanical strength: Silicon Nitride Ceramics have high mechanical strength and are resistant to mechanical wear and tear. This makes them ideal for use in heating tablets that are subject to high mechanical stress.Applications of Silicon Nitride Ceramics in heating tabletsSilicon Nitride Ceramics are used in a wide range of heating tablets for various applications, including automotive, aerospace, electronics, and medical devices. They are used in heating tablets for engine preheating, high-temperature wire insulation, and cooking appliances. Silicon Nitride Ceramics also find applications in space probes, as they can withstand the harsh conditions of space without degrading.ConclusionSilicon Nitride Ceramics are a promising material for heating tablets, and their unique properties make them ideal for various applications. They offer excellent thermal conductivity, thermal shock resistance, low thermal expansion, and high mechanical strength, making them a perfect candidate for heating tablets that require stable thermal properties over a wide temperature range. With the growing demand for high-performance heating tablets, Silicon Nitride Ceramics are poised to become the future of heating tablets.
Innovative valve technology reduces emissions and improves safety
A new innovation in valve technology has just been introduced by a leading industrial valve manufacturer – the Nozzle Breathing Valve. This latest valve innovation promises to deliver exceptional efficiency, reliability, and safety in various industrial applications, making it a popular choice among operators.The Nozzle Breathing Valve is a type of pressure-relief valve that is primarily used in storage tanks containing volatile organic compounds (VOCs). When the internal pressure of the tank exceeds the preset level, the valve automatically opens, allowing some of the vapor to escape. This mechanism keeps the pressure inside the tank within the acceptable range, preventing a possible rupture of the tank and dangerous leaks of hazardous chemicals.What sets the Nozzle Breathing Valve apart from the traditional pressure-relief valves is its unique design. The valve has two separate chambers – the upper chamber, which is designed to vent the vapor, and the lower chamber, which serves as a seal for the valve's central stem. The valve features a nozzle-shaped structure that connects the two chambers and channels the vapor to the upper chamber. This design ensures a more streamlined vapor flow, minimizing turbulence and pressure drop and reducing the likelihood of leakage.Another key feature of the Nozzle Breathing Valve is its ability to regulate the valve opening according to the vapor flow rate. This feature is made possible by the valve's spring-loaded mechanism, which responds to changes in pressure differential. When the flow rate is low, the valve's opening is minimal, maintaining a tight seal. As the flow rate increases, the pressure differential overcomes the spring force, allowing the valve to open further.The Nozzle Breathing Valve's high level of efficiency and versatility has made it a popular choice among operators in various industries. The valve is commonly used in petrochemical, pharmaceutical, and food and beverage plants, where it helps to maintain a safe and healthy working environment.According to the manufacturer, the Nozzle Breathing Valve is built to the highest industry standards, using only top-quality materials and advanced manufacturing techniques. The valve body and stem are made from stainless steel, ensuring high corrosion resistance and durability. The valve's internal components are precision-engineered to withstand the demands of harsh industrial environments while maintaining their performance and reliability.The manufacturer also highlights the valve's ease of maintenance as another key advantage. The Nozzle Breathing Valve's simple design and construction make it easy to disassemble and clean, reducing downtime and maintenance costs. The valve's modular design also makes it easy to replace damaged or worn-out parts without having to replace the entire valve.Overall, the Nozzle Breathing Valve represents a major step forward in valve technology, offering exceptional efficiency, reliability, and safety in a compact and versatile package. Its unique design and features have made it a popular choice among operators in various industrial applications, and its high-quality construction and ease of maintenance have earned it a reputation for long-lasting performance.As industries continue to face new challenges and demand higher levels of safety and efficiency, the Nozzle Breathing Valve is well-positioned to meet these demands and provide operators with the peace of mind they need to focus on their core business activities.
Common Rail Injector Tester Simulator with Piezo Injector Function - New Arrival at Taian Xinan Precision Machinery in Shandong, China
China Taian Xinan Precision Machinery has recently announced the launch of two new products in its line of advanced machinery for fuel injection systems - the CR2000 Common Rail Injector Tester Simulator with Piezo Injector Function, and the CR718 Common Rail Test Bench.The CR2000 Common Rail Injector Tester Simulator with Piezo Injector Function is designed to accurately test the performance of injectors used in modern diesel engines. It features advanced technology that allows it to simulate the high pressures and precise timing of fuel injection, ensuring that the injector is operating at its optimal level. In addition, this tester simulator is equipped with piezo injector function, which allows it to test and diagnose more advanced injectors found in modern diesel engines.The company has also released the CR718 Common Rail Test Bench, which is designed to test and diagnose the performance of the common rail systems used in modern diesel engines. This test bench can diagnose and repair failures in the common rail system by simulating the pressures and inputs needed by the engine during high-performance operation. With its advanced features, the CR718 Common Rail Test Bench is an essential tool for diesel engine mechanics and technicians.China Taian Xinan Precision Machinery is a leading manufacturer of advanced machinery for diesel engine fuel systems. With over 20 years of experience in the industry, the company has worked to continuously introduce new and innovative products that meet the needs of customers worldwide. Its products are known for their precision, reliability, and exceptional performance.The company has built its reputation on providing high-quality products and exceptional customer service. As a result, it has garnered a loyal following of customers who have come to depend on its advanced machinery for their diesel engine needs. With the introduction of these two new products, China Taian Xinan Precision Machinery is further solidifying its position as a leading provider of innovative and reliable machinery for diesel engine fuel systems.For customers interested in learning more about these new products or inquiring about pricing, the company has provided a contact email for inquiries. It promises to respond within 24 hours, ensuring that customers receive the support and information they need in a timely manner.In conclusion, the launch of the CR2000 Common Rail Injector Tester Simulator with Piezo Injector Function and the CR718 Common Rail Test Bench is an exciting development for the diesel engine industry. These new products showcase the company's commitment to innovation and excellence in manufacturing. With its reputation for quality and customer service, China Taian Xinan Precision Machinery is well-positioned to continue leading the diesel engine fuel system market.
High Quality Silicon Carbide Rollers: Trusted Supplier in China
China Silicon Carbide Roller: The Future of Industrial RollersSilicon carbide is a compound of silicon and carbon that has proven to be an ideal material for use in a variety of industrial applications. One of the most significant uses of silicon carbide is in the production of rollers, which serve as critical components in the manufacturing of various products such as ceramics, glass, electronics, and more.China Silicon Carbide Roller is a quality supplier of silicon carbide rollers that are widely used in various industrial processes. The company has been providing top-notch silicon carbide rollers for years, catering to the needs of various industries worldwide.Silicon Carbide Rollers: Properties and ApplicationsSilicon carbide rollers are highly durable and have excellent mechanical properties, making them ideal for use in industrial processes that require high-performance equipment. These rollers are made from high-purity silicon carbide ceramic, which has superior resistance to wear, corrosion, and high temperatures up to 1500°C.Silicon carbide rollers are used in various industries, including ceramics, glass, metallurgy, and cement manufacturing, to name a few. These rollers are also widely used in the electronics industry for the production of semiconductors and solar panels.Advantages of Using Silicon Carbide RollersSilicon carbide rollers offer several benefits over traditional rollers made from other materials. Firstly, silicon carbide rollers have excellent thermal conductivity, making them suitable for use in high-temperature processing environments. Additionally, they have a low thermal expansion coefficient, which ensures the rollers maintain their shape and dimensional stability over time.Furthermore, silicon carbide represents a significant improvement over traditional rollers that are made from steel or other materials that wear out quickly. Steel rollers are prone to corrosion and wear, which can lead to inefficiencies in the manufacturing process, and even product defects.In contrast, silicon carbide rollers last significantly longer than steel rollers, reducing the need for frequent replacements and the associated downtime and costs. This, in turn, leads to increased productivity and lower overall manufacturing costs.Quality Supplier of Silicon Carbide Rollers in ChinaChina Silicon Carbide Roller is a quality supplier of silicon carbide rollers based in Weifang, Shandong Province, China. The company has been providing superior-quality silicon carbide rollers to customers worldwide for years, offering a wide range of rollers that cater to various industrial needs.The company's silicon carbide rollers meet international quality standards and undergo rigorous quality testing to ensure that they meet customer expectations. They offer custom-made solutions to customers, tailoring their rollers to specific industrial needs.ConclusionSilicon carbide rollers represent an essential component in various industrial processes. They offer numerous benefits over traditional rollers, such as improved durability and wear resistance, increased dimensional stability, and higher thermal conductivity.China Silicon Carbide Roller is a leading provider of silicon carbide rollers that cater to various industrial needs worldwide. Their rollers represent the future of industrial rollers, offering superior-quality and custom-made solutions that meet specific customer requirements.
Best Water Resistant Pillow Covers of 2019: Find Your Perfect Match
Water Resistant Pillow Cover – The Ultimate Solution for Your Sleep WoesSleep is an essential part of our daily routine and it helps us to function properly. However, for some people, falling asleep and staying asleep can be a challenge. The culprits can range from discomfort while sleeping to allergies and medical conditions. One way to overcome these sleep woes is by investing in a water-resistant pillow cover. Pillow covers are used to protect your pillows from dust, allergens or spills. A water-resistant pillow cover does this and more – it not only protects your pillow from water damage but also helps keep it clean and hygienic. Water-resistant pillow covers come in a variety of materials such as cotton, polyester, and microfiber. They are designed to prevent liquids from penetrating the pillow and causing damage. This makes them perfect for people who sweat heavily while sleeping, children who wet the bed or pet owners whose pets sleep on their bed. Apart from preventing water damage, water-resistant pillow covers also keep your pillow odor-free and hypoallergenic. They prevent mold and mildew growth, which are notorious for causing respiratory problems. They are easy to wash and dry, and some brands can even be wiped clean. When shopping for a water-resistant pillow cover, ensure you choose one that is breathable, comfortable and does not make any noise when you move. It should be able to protect your pillow without altering its feel. At Pillowcover.biz, we have researched the best water-resistant pillow covers available in the market and identified the top nine for 2019. Our research is based on wear and tear tests, price, customer feedback and product specifications. Our top picks cover different price ranges, sizes, and materials. Whether you prefer a simple white cotton cover or a luxurious satin one, our top picks have got you covered. Our top pick is the AllerEase Maximum Allergy and Bedbug Waterproof Zippered Pillow Protector. This cover not only protects your pillow from water damage but also from allergens and bed bugs. The waterproof layer is coated with a polyurethane film that ensures complete water resistance. It has a zippered closure that prevents allergens and bed bugs from entering your pillow. The cover comes in two sizes – standard/queen and king and is machine washable. Another great option is the Coop Home Goods Lulltra Waterproof Hypoallergenic Pillow Protector. This cover is made from a blend of bamboo-derived viscose rayon and polyester which gives it a soft, comfortable and breathable feel. It is also hypoallergenic, has a waterproof barrier and can be machine washed. This cover fits standard, queen and king-sized pillows. If you are looking for a luxurious water-resistant pillow cover, the Royal Hotel Silky Soft Bamboo Waterproof Pillow Protector is an excellent choice. Made from a blend of bamboo-derived rayon and polyester, this cover has a silky smooth feel and is perfect for people with sensitive skin. It is waterproof, hypoallergenic and can be machine washed. This cover fits standard, queen and king-sized pillows. In conclusion, a water-resistant pillow cover is an essential investment for a comfortable, hygienic and peaceful sleep. It not only protects your pillow from water damage but also has hypoallergenic and odor-reducing properties. With our top picks for 2019, you can find a cover that suits your needs and preferences. At Pillowcover.biz, we are committed to providing our customers with quality products that offer value for money. Invest in a water-resistant pillow cover today and experience the joy of a good night’s sleep.
Discover the Benefits of High Heat Resistant Ceramics
Title: Breakthrough in High Heat Resistant Ceramics Technology Facilitates Innovation and GrowthIntroduction:High Heat Resistant Ceramics, a pioneering manufacturer in the ceramic industry, has recently achieved a significant milestone in the development of cutting-edge heat-resistant ceramics. With a strong focus on innovation and continuous research, the company has successfully created an advanced range of ceramic products that are capable of withstanding extreme temperatures, enabling various industries to optimize their processes and improve operational efficiency. This breakthrough has opened doors for groundbreaking applications in numerous sectors, such as aerospace, automotive, energy, and more.[Paragraph 1]High Heat Resistant Ceramics has consistently been at the forefront of pioneering advancements in ceramic technology. Their dedication to research and development has resulted in the creation of a diverse range of ceramic materials renowned for their exceptional durability and superior temperature resistance. These ceramics are specifically designed to operate flawlessly even at the most extreme temperatures, offering industries unparalleled reliability and performing consistently in the harshest conditions.[Paragraph 2]The company's highly specialized team of engineers and scientists invest considerable time and effort into perfecting the composition of their ceramics. Leveraging the latest manufacturing techniques and state-of-the-art equipment, High Heat Resistant Ceramics has successfully developed materials that can endure temperatures exceeding 2000 degrees Celsius. This exceptional heat resistance ensures reliability and efficiency across a wide array of industries, including aerospace propulsion systems, automotive engines, thermal power generation, and advanced electrical components manufacturing.[Paragraph 3]Recognizing the increasing demand for materials that can withstand extreme conditions, High Heat Resistant Ceramics has been working closely with industry leaders to develop custom ceramic solutions tailored to their specific needs. By partnering with these companies, the ceramic manufacturer has gained valuable insights into diverse sectors, enabling them to develop cutting-edge products that address essential industry challenges. This collaborative approach has positioned High Heat Resistant Ceramics as a trusted and reliable partner for numerous industries seeking innovative solutions.[Paragraph 4]The aerospace industry, in particular, has highly benefited from High Heat Resistant Ceramics' advancements. These ceramics find extensive applications in gas turbine engines, heat shields, rocket nozzles, and other crucial components. The remarkable temperature resistance of these ceramics ensures enhanced engine performance, reduced fuel consumption, and extended product lifecycles, ultimately resulting in significant cost savings.[Paragraph 5]In addition to the aerospace sector, the automotive industry has also been an eager adopter of High Heat Resistant Ceramics' products. Their ceramics are employed in the manufacturing of catalytic converters, exhaust systems, and various engine components. The superior heat resistance and exceptional durability of these ceramics enable automotive components to withstand high temperatures generated during normal engine operation, increasing overall efficiency and minimizing material degradation.[Paragraph 6]Looking ahead, High Heat Resistant Ceramics continues to push the boundaries of ceramic technology. Having established themselves as industry leaders in heat-resistant ceramics, the company remains committed to further enhancing the performance and versatility of their products. By investing in ongoing research initiatives, the manufacturer aims to develop ceramics that can withstand even higher temperatures, enabling industries to operate in more extreme environments.[Paragraph 7]The success of High Heat Resistant Ceramics and their groundbreaking achievements in ceramic technology reflects their dedication to innovation and meeting the evolving needs of industries worldwide. With their range of exceptional heat-resistant ceramics, the company is poised to lead the way in enabling breakthroughs across various sectors.
Nasdaq-listed home interiors company sees boost in stock prices
SiC tile, also known as silicon carbide tile, is a high-performance ceramic material that is used in a variety of applications. Its unique properties make it an attractive choice for various industrial processes, including ballistic armor, aerospace, and electronics.SiC tile is engineered to withstand extreme temperatures, harsh chemicals, and even impacts from high-velocity projectiles. Its unique combination of strength, durability, and thermal conductivity make it a standout material for a wide range of applications, especially those that require high levels of performance under challenging conditions.One of the primary uses for SiC tile is in ballistic armor. Due to its exceptional hardness and strength, SiC tile is incredibly effective at stopping bullets and other projectiles. In fact, it is often used in conjunction with Kevlar to create a lightweight, yet incredibly strong, armor system for military and law enforcement personnel.In addition to its use in armor, SiC tile is also employed in the aerospace industry. Its high thermal conductivity and excellent resistance to oxidation make it an ideal material for use in the hot sections of jet engines. In these high-temperature environments, SiC tile offers superior performance compared to other materials, resulting in increased efficiency and longer engine lifetimes.SiC tile is also utilized in the electronics industry. Its unique properties make it an attractive choice for use in high-power electronic devices, such as power inverters and high-frequency amplifiers. In these applications, SiC tile offers better thermal management than traditional materials, resulting in increased reliability and improved performance.As the demand for high-performance materials continues to grow, SiC tile is poised to become an increasingly important component across a wide range of industries. Its unique properties make it an attractive choice for a diverse array of applications, from armor to aerospace and beyond.In conclusion, SiC tile is a high-performance ceramic material that offers exceptional strength, durability, and thermal conductivity. Its unique properties make it an attractive choice for a wide range of applications, including ballistic armor, aerospace, and electronics. As the demand for high-performance materials continues to expand, SiC tile is poised to become an increasingly important component across a wide range of industries.
Two Contract Workers Suffer Severe Burns After Liquid Metal Spill at Steel Plant in Visakhapatnam
Working in a steel plant can be a challenging task as it involves handling heavy machinery and hazardous materials. One such incident happened recently where two contract workers suffered severe burns due to liquid metal spillage. The incident occurred in the SMS unit of a steel plant in Visakhapatnam.It is reported that the workers were performing their duties when suddenly liquid metal spilled on them. While some workers escaped with minor injuries, two workers sustained severe burns. The cause of the accident was the failure of the burner nozzle. When the nozzle failed, it caused a leakage of liquid metal, which resulted in the accident.Burner nozzles are essential components in steel plants as they help in the production of hot and molten metals. They are used to inject fuel and air into the furnace to generate high temperatures. If the burner nozzle is not functioning correctly or has any faults, it can lead to accidents such as the one that occurred in this steel plant.Steel plants are known for their high-risk working environments, and accidents are common. However, companies can take measures to reduce the risk of such accidents. Proper training should be provided to all workers involved in handling machinery and hazardous materials. Workers should be equipped with the necessary safety gear such as helmets, gloves, and protective clothing.Regular maintenance and inspection of machinery and equipment should be carried out to ensure their proper functioning. This can prevent accidents caused by faulty machinery. It is also essential to create a culture of safety in the workplace, where workers are encouraged to report any hazards or faults in machinery.In conclusion, accidents can happen in any workplace, but they can be avoided by taking proper safety measures. The incident in the steel plant in Visakhapatnam highlights the importance of ensuring the proper functioning of machinery and equipment in high-risk environments. Burner nozzles play a crucial role in steel plants, and their maintenance and inspection are necessary to prevent accidents. By implementing safety measures, companies can provide a safer working environment for their employees, reducing the risk of accidents.